Akron Ceramic Design Guide
General
- Technical Ceramics should be designed with a configuration as simple and regular as possible.
- Round parts have a lower tooling expense than other shapes.
- Avoid undercuts that require split molds.
- Avoid large variations in thickness of cross-sections. Chamfers on corners and edges reduce chipping during de-scaling and enhance appearance.
- All parting lines (around part periphery and holes) have scale that requires removal prior to firing.
- The addition of glaze (ceramic coating) improves appearance and aids in cleaning of surfaces. The use of glaze also retards the speed in which moisture is absorbed into the ceramic part.
Cross-Sections
Try to maintain uniform wall sections to reduce the potential of cracking during the drying/firing process. Inconsistent wall sections will result in cracking of parts, thus increasing the amount of scrap.
Vertical Projections
The higher the wall section, the thicker the section must be to properly support ejection from he mold. Allow for 2° of draft on internal walls. External walls of parts can be straight (no draft).
Holes/Counterbores
Keep holes to a minimum of 0.060″/ Thru-holes do not require draft. Blind holes need 2° draft (1° minimum). Avoid rectangular or oval holes due to machining requirements for spares. Oval holes can be used with success to offset shrinkage concern where mounting holes are critical.
Grinding
Where part thickness/flatness is critical, small grinding pads can be added as stock to be ground. This feature requires a secondary operation and will add to the cost of the part.
Tolerances
Take care in ensuring that tolerances are developed for functional performance of the part, Ceramic tolerances need to be designed as liberal as possible and if accomplished will yield a lower-cost part.
Standard Tolerances
Pressed ware: +/- .015″ per inch, minimum of +/- .015″, add +/- .005″ for each glazed surface, add +/- .031 for pressing dimensions.
Injection molding: Divide the above tolerances by a factor of three, for example use +/- .005″ per inch.
Tolerance Example:
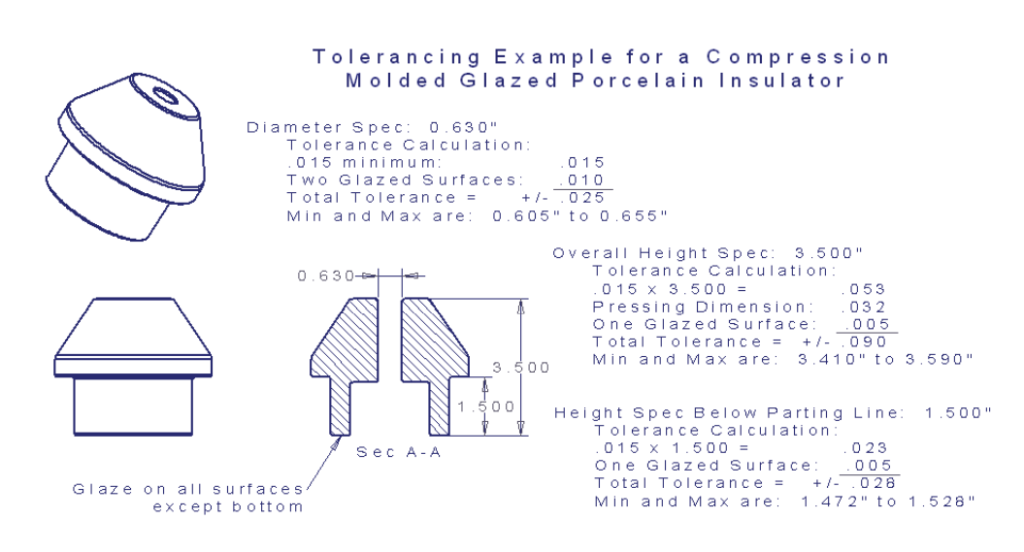
Contact sales@akronporcelain.com today to discuss your next mold design!
Industries Served
Electrical Distribution, Foundry, Major Appliance, Commercial Lighting, Water Filtration, Medical, Oil & Gas, Automotive